Trends in the Mining Industry
CyientTrends in the Mining Industry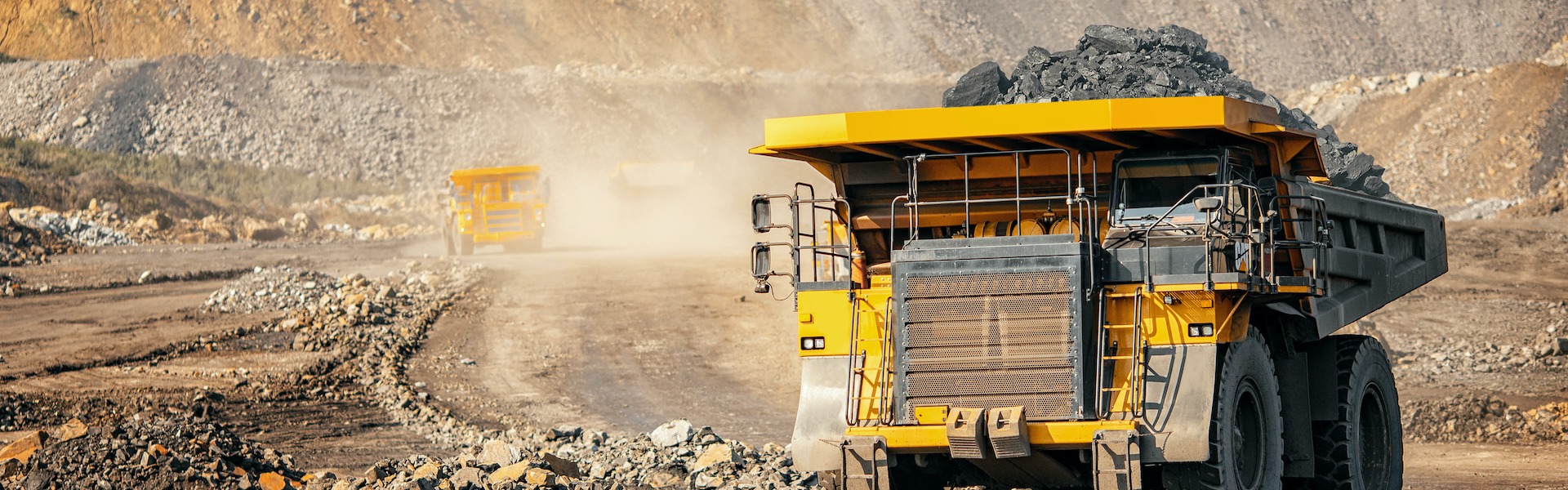
Introduction
The mining industry plays a critical role in any developing economy. Being the base for almost all supply chains, its performance reflects the socio-economic well-being and development of a nation. Mining is a challenging industry even in the best of times. Issues like demand volatility, price drops, decreasing ore grades, deeper deposits, harder rock mass, strict labor market, and increased cost due to enhanced standards of production have added to the traditional challenges of the industry. For years, mining saw limited technological advancements, adding to the woes of the industry.
Over the last few years, most companies have made the necessary investments. As a result, new processes, equipment, and technologies such as drones, virtual reality, autonomous vehicles, remote monitoring, and electric vehicles are reshaping the mining industry today. Technologies like remote asset management through drones, advanced analytics and sensors are contributing to reduced maintenance cost and downtime. Use of robotics and semi-autonomous equipment has improved reliability, safety, and productivity while significantly reducing costs and risk.
Drones
The increased use of drones for exploration, survey and mapping, equipment inspections, safety, and security has greatly simplified these activities. Open-pit mining operations are carried out with heavy duty industrial equipment and are deployed in a wide work area. Such heavy equipment needs periodic inspections in order to ensure breakdown- free operations. These inspections can be expensive, time-consuming, and require a highly skilled workforce. Drones can be the perfect solution in this scenario. Inspections through drones is highly efficient and safe, and the data quality from these drones is often superior.
The workers in the mining industry operate in an extremely high-risk environment. Deep underground activities are subject to hazards like rockfall, extreme humid conditions, gas leaks, dust explosions, and floods.
Underground drones flying through mines to search caves, collect data, and aid in the mapping process offer a huge advantage. They have proved to be extremely effective at eliminating the need to send human surveyors for activities such as recording gas levels, identifying geological features, and recording high-quality visuals of cave interiors. In an underground setting post excavation, there are multiple risks like potential collapse, inaccessible areas, and no light. Drones can familiarize workers with such new and volatile work environments, helping them prepare for possible hazards.
Underground or indoor drones are also used to inspect equipment. Indoor drones can fly through and around stockpile feeders, mills, flotation cells and crushers, collecting high quality visual data. Most of the times the data collected by the drones is superior to data collected manually.
Inspection data collection through drones instead of manual inspection can also eliminate the stoppage of operations for inspection.
Some of the major players in this area are Airobotics, Emesent, Airware, and Microdrones.
Airobotics
Airobotics has developed an automatic, on- demand solution for collecting aerial data in mining facilities without the logistics involved in drone operations. This autonomous drone streamlines operations, increases efficiency, and offers immediate, easy access to the required data.
Emesent
Emesent, a drone autonomy company, in association with Hovermap, developed a LiDAR mapping and autonomy payload, providing a complete solution for inspection and mapping of underground mines, transport tunnels, and utility tunnels.
Airware
Airware, the international drone solutions provider, together with SenseFly, developed the eBee X fixed-wing drone with mining data analytics platform Redbird, offering many services and solutions.
Microdrones
Microdrones offers services to the mining industry through the mdLiDAR and mdMapper series of drone surveying equipment. These drone systems make it easy to collect and process data, and maintain digital twins of mining sites.
Cyient has developed advanced drone tech solutions for the industry. Its Vegetation Management Solution leverages LiDAR and imagery data of the area of interest (AOI), processes them to create an as-built (3D World) model, and then runs powerful analytics to derive clearances of vegetation and other man- made objects from the power lines to identify hazards.
Cyient's Virtual Asset Management Solution leverages imagery data captured of the asset through drones and runs on fully automated machine learning and deep learning capabilities such as object and defect detection algorithms. Drone technology coupled with Cyient’s new solutions helps various industries such as power transmission and distribution, telecommunications, rail networks, wind power companies, mining, etc. make informed decisions, and improve or replace manual inspection programs.
Virtual Reality
Virtual reality (VR) is a three-dimensional, computer-generated environment that humans can explore and interact with. It is a rapidly growing technology used for training and simulation. It proved highly effective in critical areas such as training astronauts for space travel, exploring the intricacies of miniature objects, training medical students to practice surgery on computer-generated subjects, as well as in various activities of the mining industry.
The perils of the work environment of mining workers are well known. Many mining fatalities are caused by insufficient training. Adequate training in a real mining environment offers only limited real-time situations. Many real-time situations are difficult to explain and train for in classrooms. VR facilitates the development of virtual environments to allow mine personnel to practice and experience mine situations, day-to-day activities, and processes at a mining site. It provides an opportunity to explore the diverse and disparate information associated with mining processes. VR-based training can expose people to real working situations without the associated risks. It helps train mining operators effectively to improve safety, increase productivity, and reduce costs.
Use of explosives for blasting is a critical activity fraught with extreme risk. A simulated or VR mine helps trainees to learn and practice explosive placing, setting, and detonating in a safe environment. All mistakes are captured and reviewed as learning opportunities without causing any damage to people, equipment, or mines.
Many miners from countries like Australia, China, Canada, and the United States are using virtual reality for training and assessment purposes.
Cyient, as an AR/VR ecosystem partner, helps in the development of virtual reality and augmented reality applications for business acceleration. Our team of digital experts combines industry expertise with years of experience in mixed reality technologies, gaming applications, learning content development, and software and programming to deliver effective solutions that maximize customer benefits. Cyient partners with industry leaders to bring high-quality 3D experiences with industry-leading AR/VR headsets along with content management, support, and upgrades to their customers/ partners.
Autonomous Vehicles
An autonomous vehicle, or a driverless vehicle, is one that is able to operate itself and perform necessary functions without any human intervention through the ability to sense its surroundings.
Hazardous operating conditions in the industry cause most of the incidents and accidents involving vehicles of all types. These can have a cascading effect leading to loss of human lives, damage to assets, and production interruption.
The mining industry is making continuous efforts to eliminate human-operated vehicles by using autonomous vehicles, which have become increasingly prevalent over the past few years. Mining equipment manufacturers like Cat, Komatsu, and Hitachi offer automated systems to their clients. These autonomous trucks use artificial intelligence (AI) and IoT technologies, and can operate 24/7 with no need for driver breaks or shift changes. Autonomous vehicles have the potential to cut operational costs tremendously while simultaneously increasing productivity and mine-site safety. They use a combination of sensors, radar, and GPS to navigate around a pre-defined course from loading units to dump locations. These include waste dumps, stockpiles, and crushers. These driverless trucks can do the same work as a skilled truck driver with no limitation as to location, time of day, or weather conditions.
Data sent by these connected, automated mining vehicles is made available to the repair crews and automated health monitoring systems. The AI algorithms in the health monitoring system can identify the system or components that are likely to fail in advance for a proactive maintenance. This type of predictive maintenance enhances the availability of vehicles and equipment, significantly improving productivity and reducing cost.
Some of the offerings of major players in automated vehicle systems are discussed below.

Caterpillar offers its Automated Haulage System (AHS) Cat® MineStarTM to optimize miners’ loading and hauling operations, keeping the shovels busy and the trucks on the move. MineStar fleet management tools will identify the opportunities to improve truck efficiencies in ways that maximize payload, reduce cycle times, lower costs, and boost profitability.
CAT claims that their solution reduces operational costs of mines by 20% and improves productivity by 30%, while reducing safety-related incidents by 50%. Fortescue Metals Group (FMG) and BHP are two of the biggest customers of Caterpillar’s autonomous haulage solutions.
Komatsu offers its Autonomous Haulage Systems (AHS), FrontRunner, for effective mine management. The FrontRunner system is designed to enable manually operated equipment (such as loaders, dozers, graders, light vehicles, etc.) to safely interact in an Autonomous Haulage Trucks (AHT) environment to further optimize the mining operation. Komatsu claims 15% reduction in operating cost while enhancing tyre life by 40%.
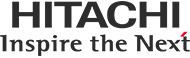
Hitachi has developed an autonomous driving system for dump trucks that is able to operate continuously even in difficult communication environments by utilizing a permission control technique inspired by the railway industry.
Scania’s new autonomous truck concept SCANIA AXL is a major step forward in the development of future vehicles. The fully autonomous Scania AXL concept is tailored for heavy duty operations and known for robustness and strength. Scania and Rio Tinto are collaborating on new-generation autonomous trucks at the latter’s Dampier Salt operations in Western Australia.
Sandvik offers two product groups as part of its advanced mining automation and tele operation solutions portfolio, “AutoMine” and “OptiMine.” The AutoMine product portfolio provides an autonomous loading and hauling solution for underground hard rock mining. OptiMine, a comprehensive suite of software platform solutions, analyzes and optimizes underground mining processes.
Cyient, with a focus on accelerating digital transformation for industries, helps customers drive business outcomes with new tools and technologies. Cyient collaborates with digital map developers to help them solve real-world issues in the automotive sector and make self- driven vehicles safer and smarter.
With more than 20 years of industry experience in semiconductor systems and software, Cyient specializes in automotive silicon and software design solutions as well as services worldwide. We have hands-on industry experience in end-to-end automotive embedded systems development, including infotainment systems, advanced driver assistance systems (ADAS), and connected car technology with functional safety ISO26262-compliant automotive systems with adaptive AUTOSAR.
Remote Monitoring / Remote Asset Management
Remote asset management solutions help improve the reliability and availability of assets. Reduction of downtime and operation at peak performance minimize risks and operating costs. Remote control technology requires human operators for most machine functions, but removes the operators from the equipment itself. These applications enable operators to work from a safe location that is far removed from the actual work site.
Remote monitoring enables collection of operational data of the equipment using a variety of sensors. These systems are able to collect, communicate, and analyze huge amounts of data in real time. This can be converted into controlling or preventive actions to avoid potential failure of equipment thereby providing complete solutions.
Many large miners across the globe are using remote monitoring solutions to monitor and control equipment and processes on a daily basis. Premier mining equipment manufacturers such as CAT, JOY and Laird have already developed sophisticated systems which make this possible.

MineWare’s Global Integrated Support Centre (ISC) is an example of advances in remote monitoring technology. They monitor and support over 250 draglines and shovels around the world, 24/7.
Sandvik remote monitoring enables supervisors to manage processes and communicate with surface and underground equipment from the safety of their control room.
AVEVA’s Asset Performance Management (APM) solution adds value to the asset life cycle helping avoid unpredicted downtime, increase asset utilization, and deliver increased value across all assets of a mining enterprise.
Electrric Vehicles
Like most other industries, the mining industry is in transition to ensure a clean energy- powered world. One of the most important aspects of this transition is the use of electric vehicles. These are considered an effective way to reduce the facility’s carbon footprint and to improve safety in the industry. Electric vehicles are better suited for underground mining operations than their fossil fuel-guzzling counterparts. They make a huge difference to air quality in the mines since they do not emit any harmful gases and particulates.
Emissions such as nitrogen oxide, carbon monoxide, and suspended particulates pose serious respiratory hazards that are invariably associated with internal combustion engines.
Further, electric vehicles radiate less heat, reducing the risk of engine overheating causing hot surfaces on equipment. They vastly reduce the exposure of workers to noise pollution, leading to improved health and safety during their duty hours.
Miners across the globe are working on strategies and pathways to achieve a low- carbon future across all their operations in alignment with the Paris Agreement. Miners are working to develop low-emission alternatives for mobile fuel use in haul, load, and rail. Diesel for trucks and electricity are the main sources of carbon emissions. In order to reduce carbon emissions, the preferred technology pathway targets a full battery electric fleet with dynamic, fast-charging facilities to maintain fleet productivity. The capacity of the battery and the endurance to work throughout the shift without a recharge are major challenges in the development of the battery-operated electric vehicles.
The development and success of electric mining vehicles also depends on enabling and associated technologies. Technology advancements in battery technology with respect to electric range, energy, power capacity, and charging time will continue to drive miners to use electric mining vehicles. Mining vehicle manufacturers like Atlas Copco, Sandvik, BYD, Komatsu, and Caterpillar are all in various stages of development of electric loaders, trucks, and associated equipment.
The Z50 Haul Truck with a 50-tonne payload capacity is the largest known battery-powered underground truck. It is equipped with AutoSwap which makes battery swapping faster and easier with a minimum amount of manual handling. Changing the battery only takes about six minutes.
The new Cat® R1700 XE LHD, with its 15-tonne payload and 24,190-kg lift and tilt breakout, features a zero-emission battery electric design that delivers superior productivity in underground applications.
Conclusion
In the midst of the momentous transition to a greener, safer, carbon-free world, mining companies are leaving no stone unturned to do their bit. The extensive use of digital technologies, automation, robotics, remote monitoring, IoT, analytics, and digital twins, among others, is helping them remain relevant, competitive, sustainable, and safe. The development and implementation of these technologies in the mining industry creates large scale opportunities for potential cooperation between the services sector and the mining industry.
As an engineering services provider, Cyient is working closely with the industry experts, mining customers, and equipment manufacturers to align the mining industry trends through our focus areas of megatrends "Data AI & Platformization", "Nextgen Connectivity Solutions," and "Intelligent & Connected Products".
About Cyient
Cyient (Estd: 1991, NSE: CYIENT) is a leading global engineering and technology solutions company. We are a Design, Build, and Maintain partner for leading organizations worldwide. We leverage digital technologies, advanced analytics capabilities, and our domain knowledge and technical expertise, to solve complex business problems.
We partner with customers to operate as part of their extended team in ways that best suit their organization’s culture and requirements. Our industry focus includes aerospace and defense, healthcare, telecommunications, rail transportation, semiconductor, geospatial, industrial, and energy. We are committed to designing tomorrow together with our stakeholders and being a culturally inclusive, socially responsible, and environmentally sustainable organization.
For more information, please visit www.cyient.com