Software-Defined Plant Operations: The scale-up has started
Written by Nilesh Auti 05 May, 2025
Software-defined is reshaping how the Industry 4.0 world runs—quietly, powerfully, and everywhere. From factory floors to control rooms, it’s not just about technology; it’s about unlocking agility, intelligence, and speed where it matters most. We’ve seen software redefined Automotive and network —and now, it is transforming how plants operate. We're moving away from rigid, hardware-bound systems and stepping into a new age where decisions happen at the edge, scale happens in the cloud, and value is delivered in real time. This is a true industry 4.0 evolution—scaling up, in motion, and on purpose.
The Industrial Opportunity Is Massive—And Mostly Untapped
Across the world, there are an estimated 14.5 million industrial establishments—spanning 10.7 million factories, 3.3 million warehouses, 50,000 transport hubs and ports, 10,000 military bases, 8,000 oil & gas fields, 47,000 power plants, 140,000 utility plants, 54,000 mines, and 263,000 hospitals and labs (Source: Harbor Research, IDC). These assets represent a $4.5 trillion optimization opportunity.
Despite momentum over the past five years, Industry 4.0's full potential remains largely untapped. Adoption has been uneven, with limited use cases and high costs slowing meaningful ROI. But that’s changing fast.
Why Now: The Three Tech Shifts Enabling Software-Defined Plant Operations
The shift isn’t about reinventing Industry 4.0. It’s about making it scalable, affordable, and intelligent. Three developments are turning that promise into reality:
- Cloud adoption is accelerating transformation: It’s now the backbone of modern plant operations—scalable, secure, and fully embraced by engineering and industrial teams.
- The network is finally industrial-grade: Affordable LTE, private 5G, and increasingly robust OT security make the backbone of smart operations viable, even in remote or brownfield locations.
- AI at the edge is going from buzz to business: AI and ML are now embedded in sensors and control systems, enabling instant decisions where timing matters most. The cloud complements this with deep analytics and strategic optimization, powering a smarter, faster industrial model.
Edge + Cloud = New Operating System for the Plant
Old plant operations relied on rigid architectures—on-prem systems running SCADA, MES, and other legacy tools, all tied to vendor-specific hardware. What we’re seeing now is a move toward multi-access edge compute and cloud-native architectures. The new sweet spot is between the L2 edge (smart sensors, embedded decision-making) and the L5 cloud (planning, optimization, AI models).
We're seeing real-world use cases adapt to this architecture—edge devices are handling automation and quality control, while the cloud is taking over tasks like planning, optimization, and predictive maintenance. Plant automation and quality monitoring are being handled at the edge. Inventory planning, energy optimization, and workforce coordination are shifting to the cloud. It’s not just more efficient—it’s dramatically more scalable.
The Market's Moving—and Fast
This isn’t just theory. According to a report by MarketsandMarkets, the global industrial software market size was valued at USD 21.5 billion in 2024 and is estimated to reach USD 46.6 billion by 2029, growing at a CAGR of 16.7% during the forecast period 2024 to 2029. Siemens, Aveva, Honeywell, Rockwell, and others are doubling down on cloud-native offerings. Just last year, Siemens acquired Altair for over $10 billion. Aveva launched its cloud platform. Microsoft and AWS are now entrenched as industrial cloud partners.
Industrial services—covering everything from network infra to data platforms—are growing just as fast. This is the segment Cyient is targeting with its software-defined plant operations play.
Where the Value Really Lies
Revenue growth is only part of the story. The real value lies in enabling affordable Industry 4.0 at scale. The new goal isn’t to rip and replace—it’s to modernize brownfield sites, transition from L3-L4 to L2-L5, and do it with measurable ROI.
That means picking the right tech stack and the right partners. Hyperscalers like AWS and Microsoft are key. So are industrial platforms with real momentum. Cyient’s focus is on high-impact sectors like:
- Energy: Modernizing brownfield oil and gas assets, enabling green hydrogen plants.
- Utilities: Especially in ANZ and the U.S., where public investment drives OT upgrades.
- Ports: Airports and seaports are shifting toward autonomous operations.
- Mining: Sustainability is pushing electrification and automation, especially in greenfield sites across Africa and South America.
The Workforce Is Evolving
In 2018, the number of industrial workers peaked, around 475 million globally. Since then, there’s been a steady shift. Today, about 30% of the industrial workforce is working on robotics, automation, and plant software. These are not fringe roles—they’re becoming the center of how modern plants run, and this shift is only picking up speed.
Smart sensors, software-defined networks, and AI-driven control rooms create demand for new skills, not eliminate jobs. The control room isn’t just remote anymore—it’s intelligent. That shift is unlocking entirely new layers of efficiency and innovation.
Moving from Vision to Reality
Software-defined operations are no longer a concept—they're a competitive edge. With edge intelligence, cloud scale, and secure networks, the industrial world is finally wired for smarter, faster, and more resilient performance.
Now’s the time to shift from legacy to leadership. The blueprint is clear. Let’s build it.
Let’s reimagine industrial performance—one data-driven decision at a time.
About the Author
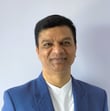
Nilesh Auti
SVP & Technology Market Maker at Cyient
Nilesh Auti is a seasoned technology and digital transformation leader with 24+ years of experience in scaling PE-backed portfolios and driving global innovation. Currently SVP – Digital & Tech Advisory at Cyient, he has previously held leadership roles at NewRocket, Tech Mahindra, IBM, and more. A recognized industry expert, he advises global councils like WEF and IIC on manufacturing, IoT, AI, and sustainability. With expertise in engineering cloud, digital manufacturing, and intelligent product design, he specializes in integrating M&A firms, building synergies, and driving large-scale transformations.